
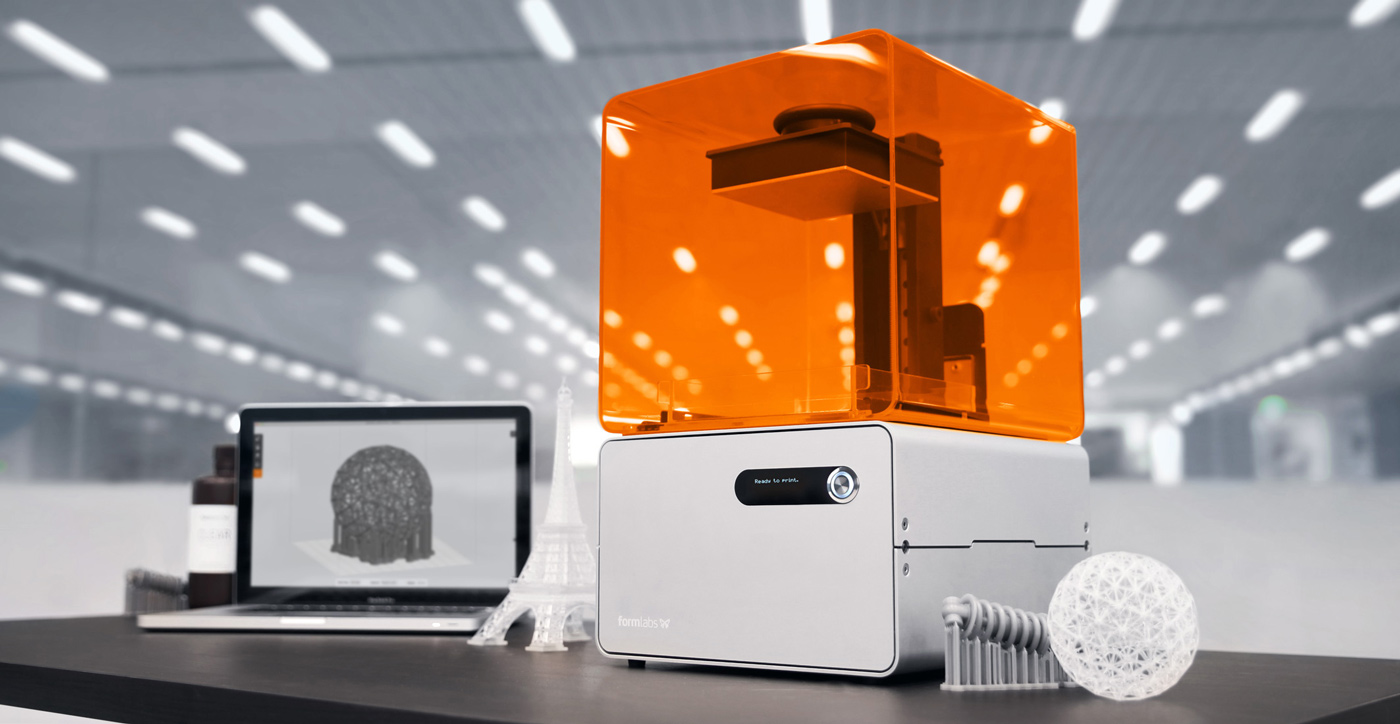

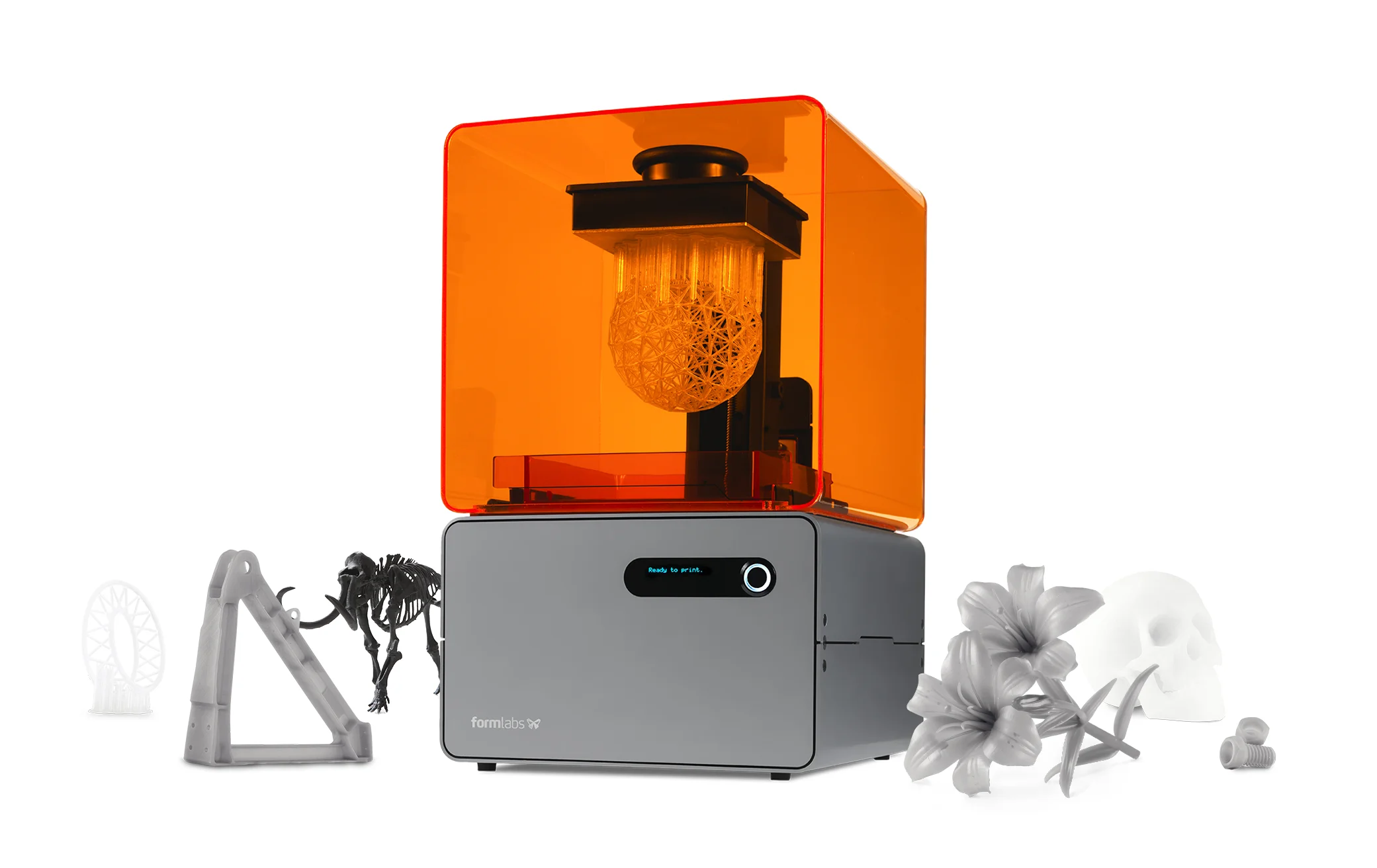
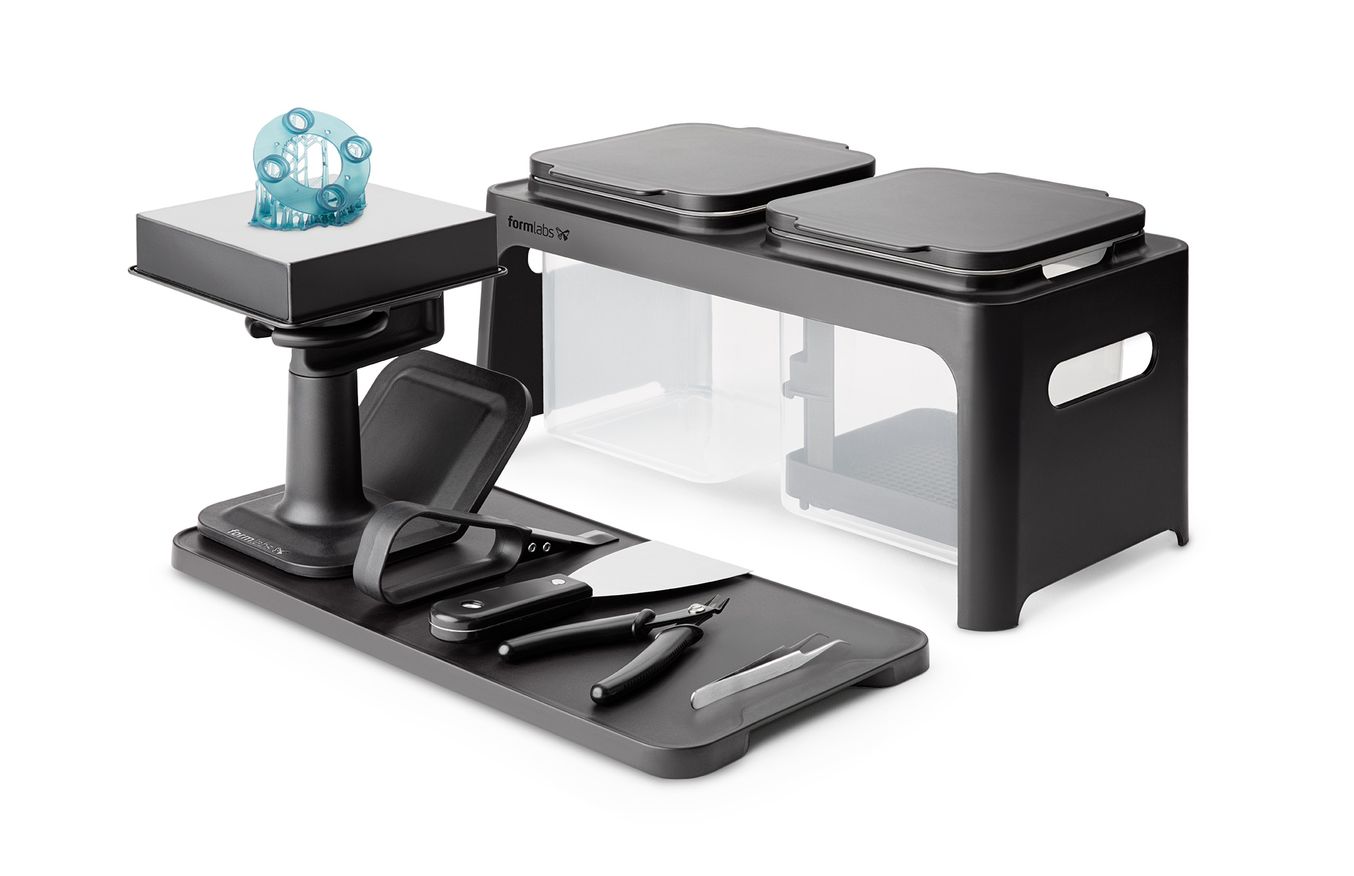
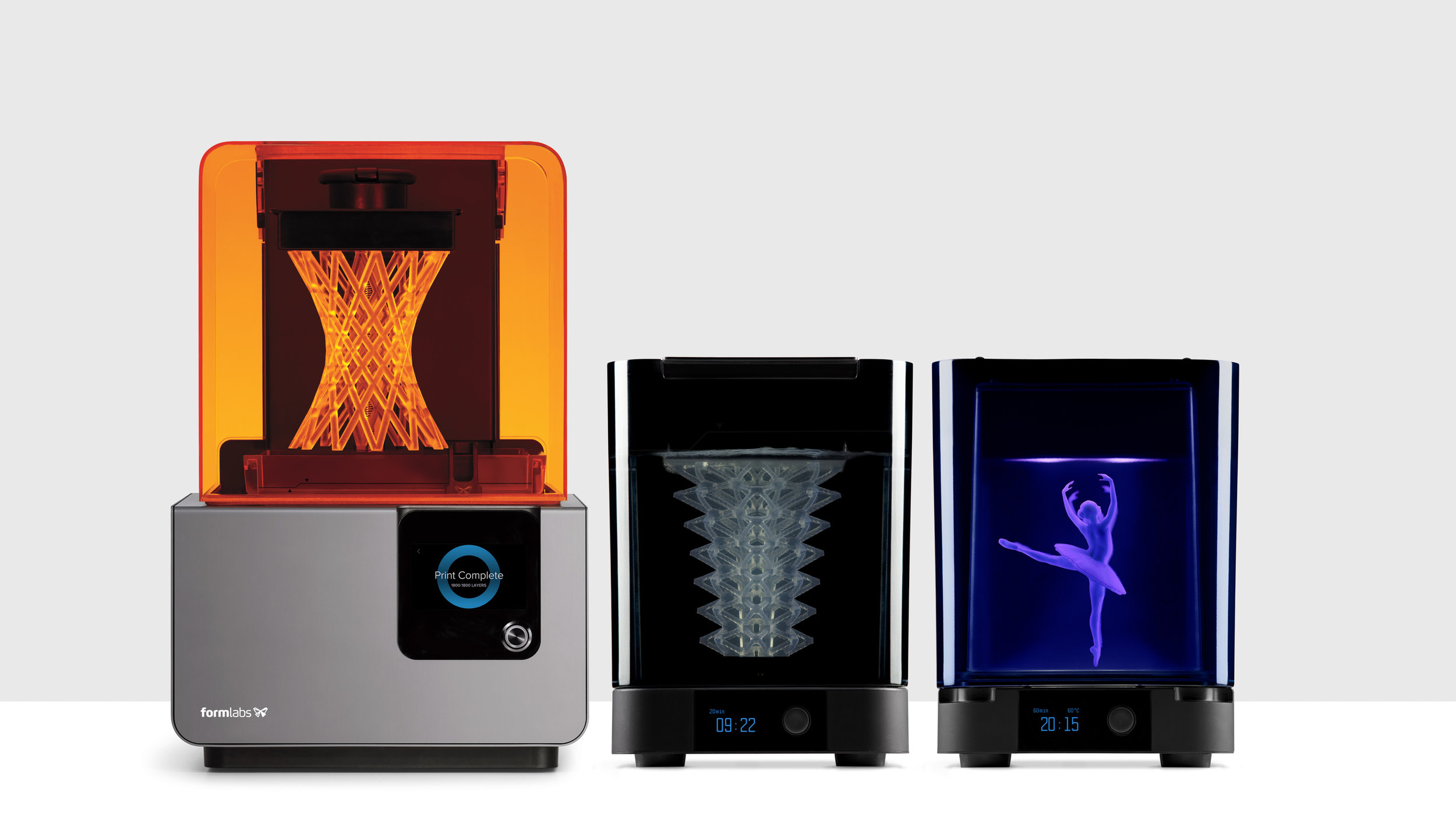
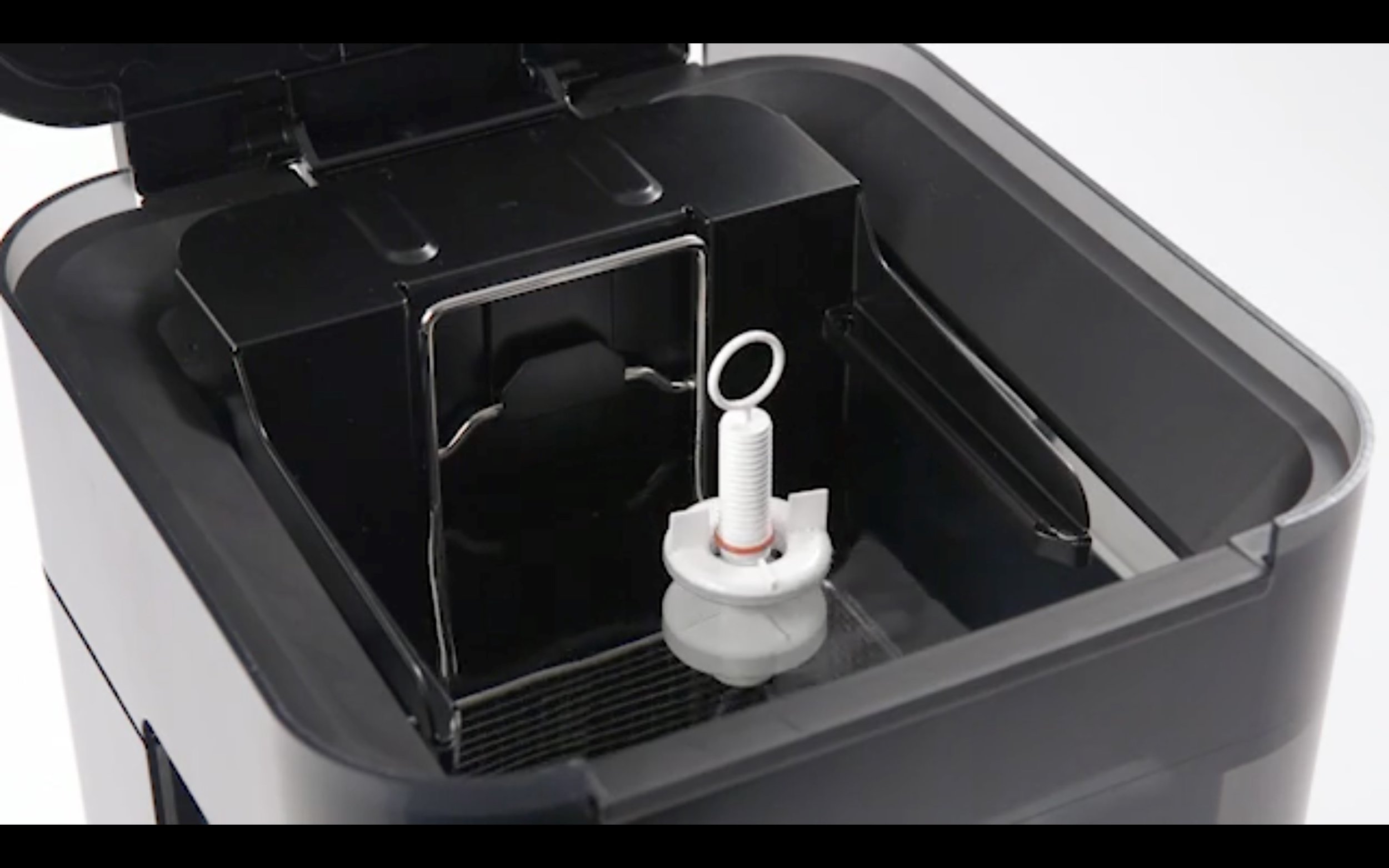
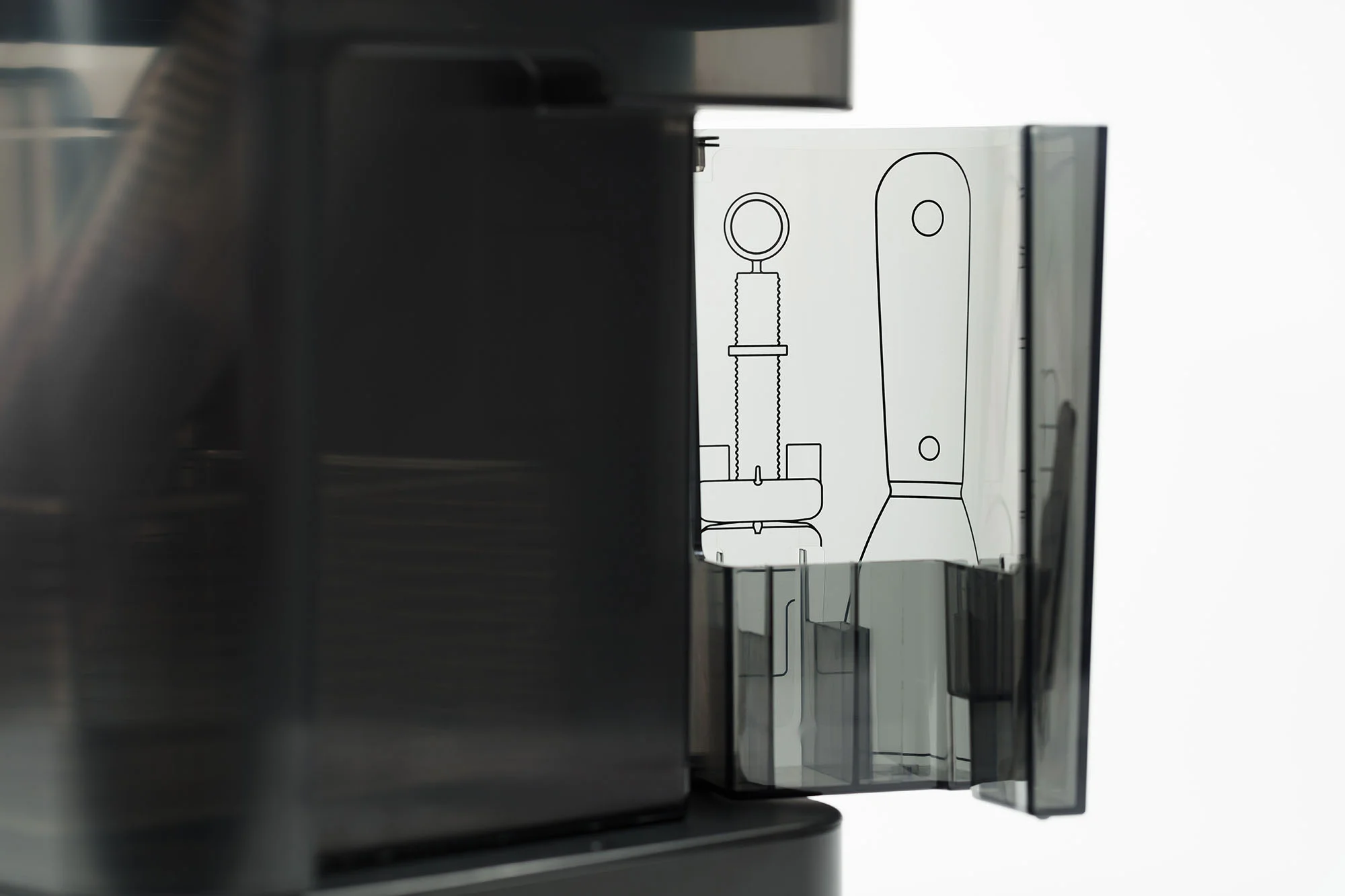

Form 2, Form Wash, and Form Cure (and Caitlin Reyda, Formlabs engineer)
Watch a recent review of the Form Wash and Form Cure from Adam Savage’s Tested here
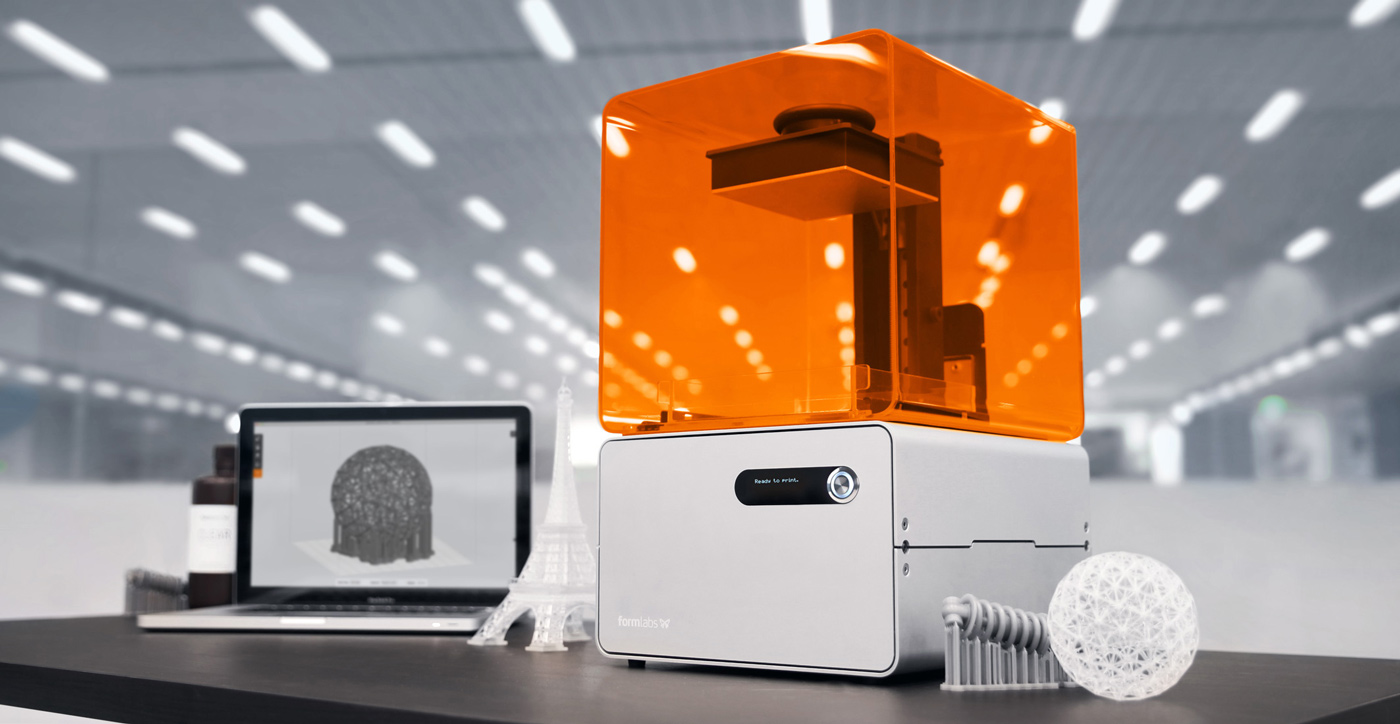
The Form 1 launched on Kickstarter in the Fall of 2012. Shortly after, the form of the orange cubic cover and bent sheet metal body with distinctive part break were showing up on other desktop stereolithography 3D printers from around the world and the shape and mechanisms behind the build platform and resin tank became industry standards.

A close up of a Form 1+ printing showing many of the parts I designed; build platform assembly, orange injection molded resin tank with min/max fill line, cover, and even the printing example part (a “Dymaxion Lattice” named in honor of R. Buckminster Fuller)
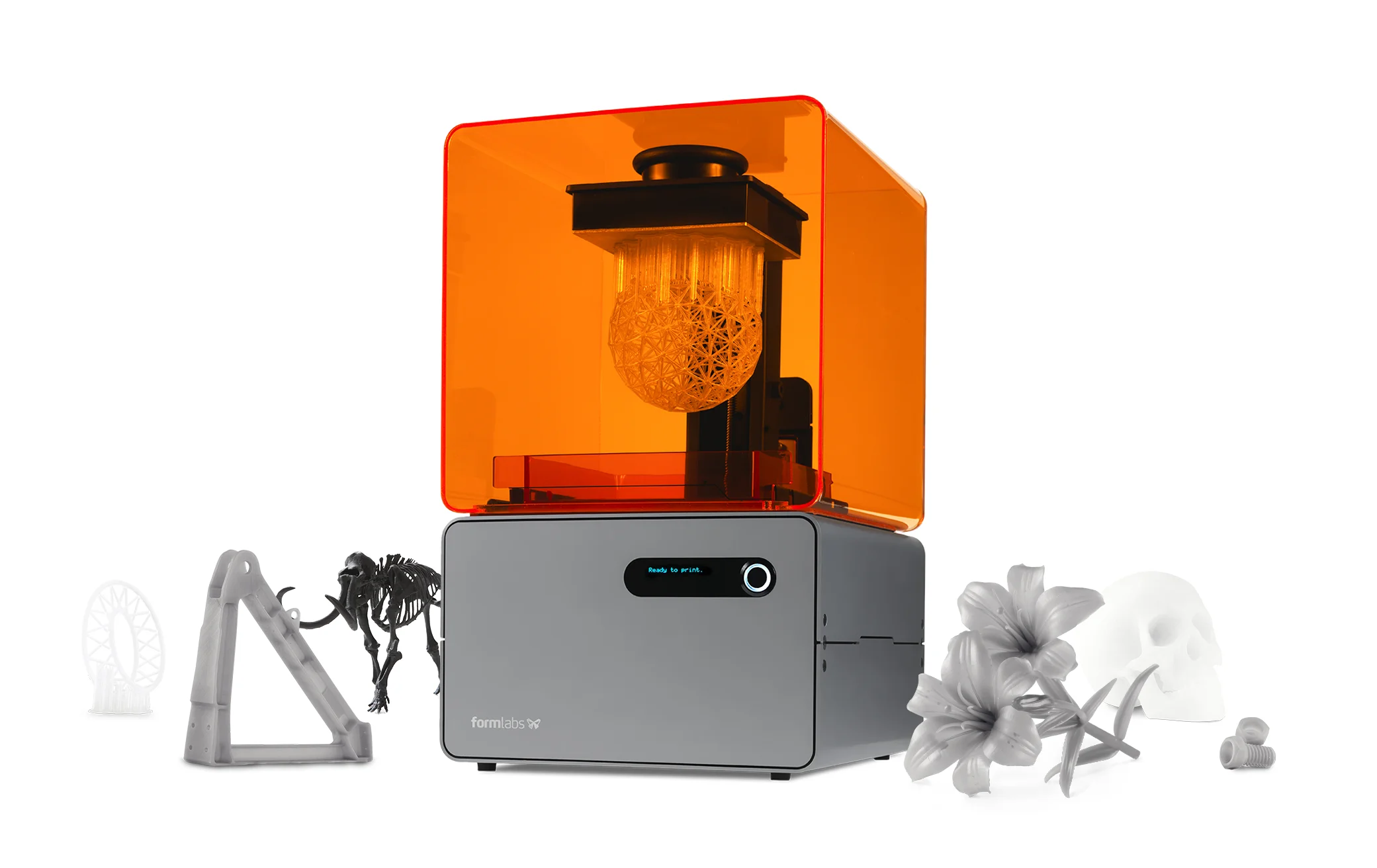
The launch of the Form 1+ presented an interesting communication design challenge; inside the machine, every critical system was massively upgraded, but with the exception of the “all-new light-blocking injection-molded resin tank,” none of these changes were visible to the customer. At the same time, we didn’t want to confuse customers since the basic operation of the machine remained unchanged and the market was becoming flooded with low-cost “homages” to the Form 1 so the Form 1+ needed to look like the massively more reliable upgrade that it was (and not a knockoff of ourselves)
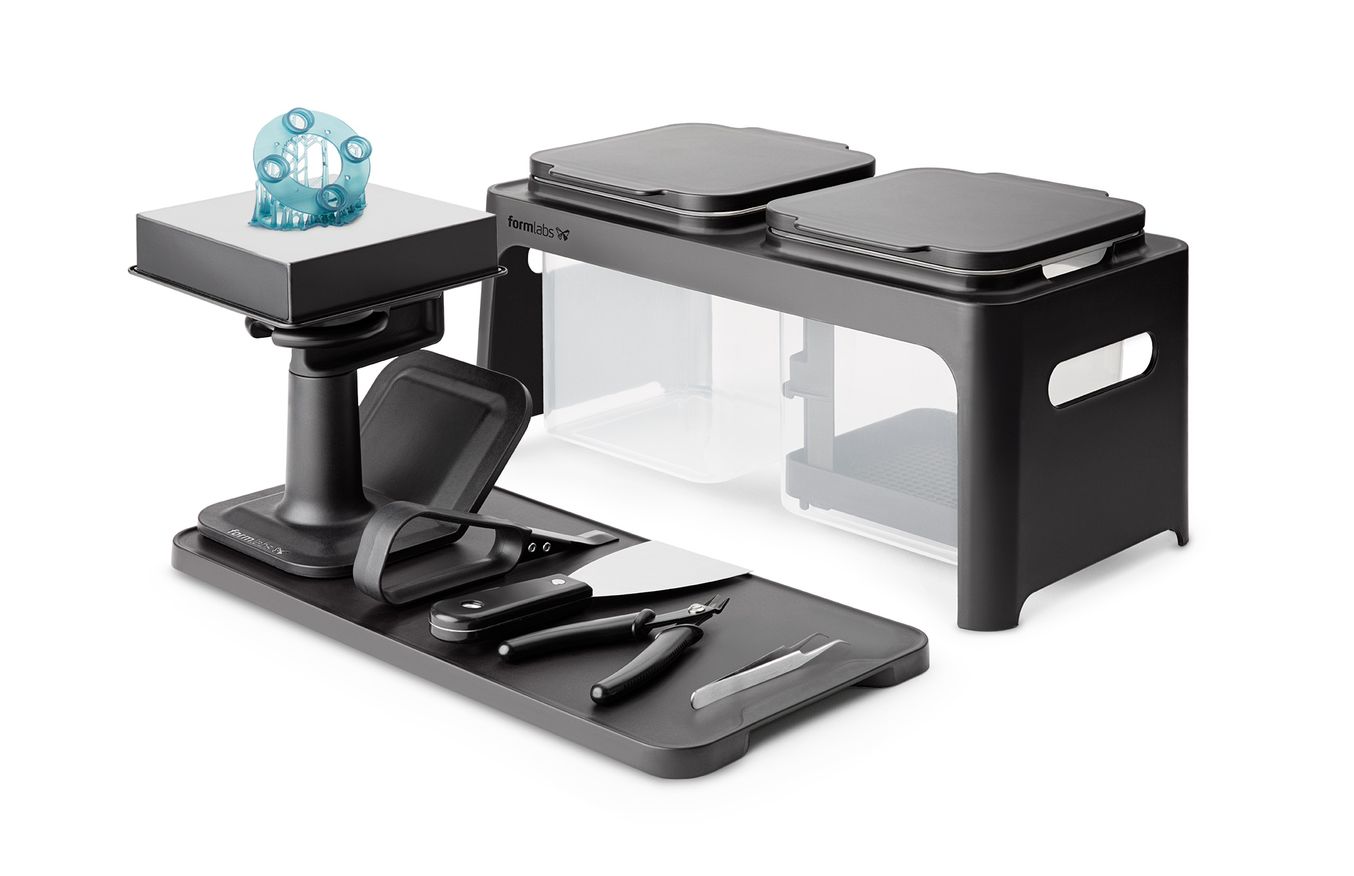
This is the finish kit shipped with every Form 2. It includes a custom part removal tool that removes parts effectively while protecting the hand, a build platform jig that holds the build platform during part removal, a one-handed rinse basket, and lids that snap into their open positions. The whole system is a much more modular, tidy, and customized solution, that takes up drastically less desk space. It was the result of years of interviewing Form 1 users in their workspaces and carefully documenting their processes, techniques, and messes.
Stand (Form 2 Finish Kit); US D777251 S1
Rinse basket (Form 2 Finish Kit); US D796763 S1
Wash station (Form 2 Finish Kit); US D804748 S1
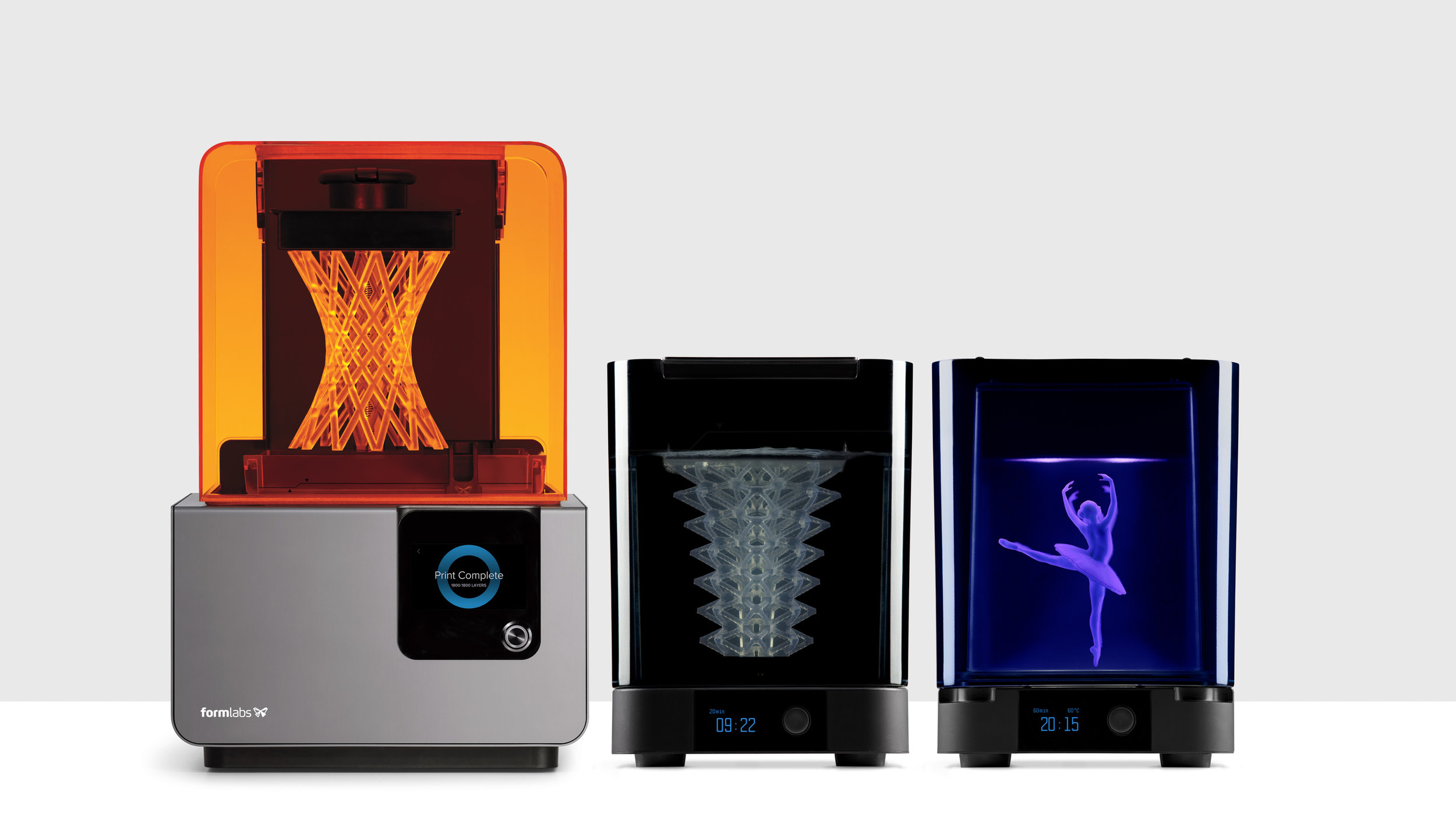
Form Wash and Form Cure were carefully designed to directly reference each other (like a matched set of salt and pepper shakers), relate to the Form 2 (exist within the same ecosystem), but not be mistaken for a new printer or a required step of the process. “Built to complete the stereolithography experience, Form Wash and Form Cure streamline the entire 3D printing process to produce more consistent results with less time and effort”
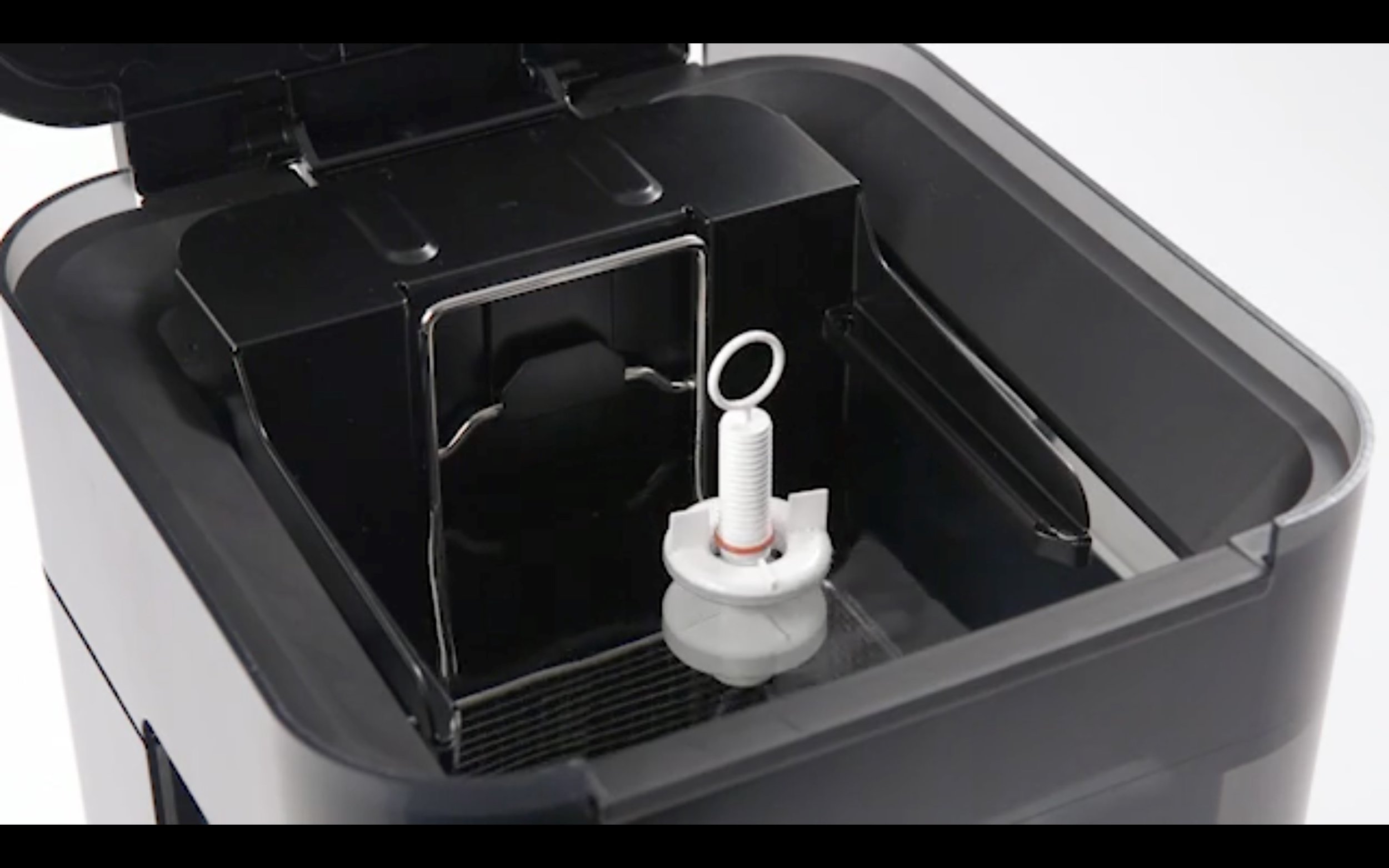
The interior of Form Wash has a fork, which holds the Form 2 build platform, as well as a removable rinse basket to hold parts separate from the build platform, to allow for the multitude of different workflows our customers had developed since Form 1 (and to maintain backwards compatibility with the Form 1 build platform).
The hydrometer is a precisely tuned scientific measurement device with a novel form factor that measures the density of the cleaning solution to let you know when to add fresh isopropyl alcohol.
These systems specifically required multiple rounds of user testing on the fork, basket, and instructional materials and resulted in UX tweaks up until the first production run.
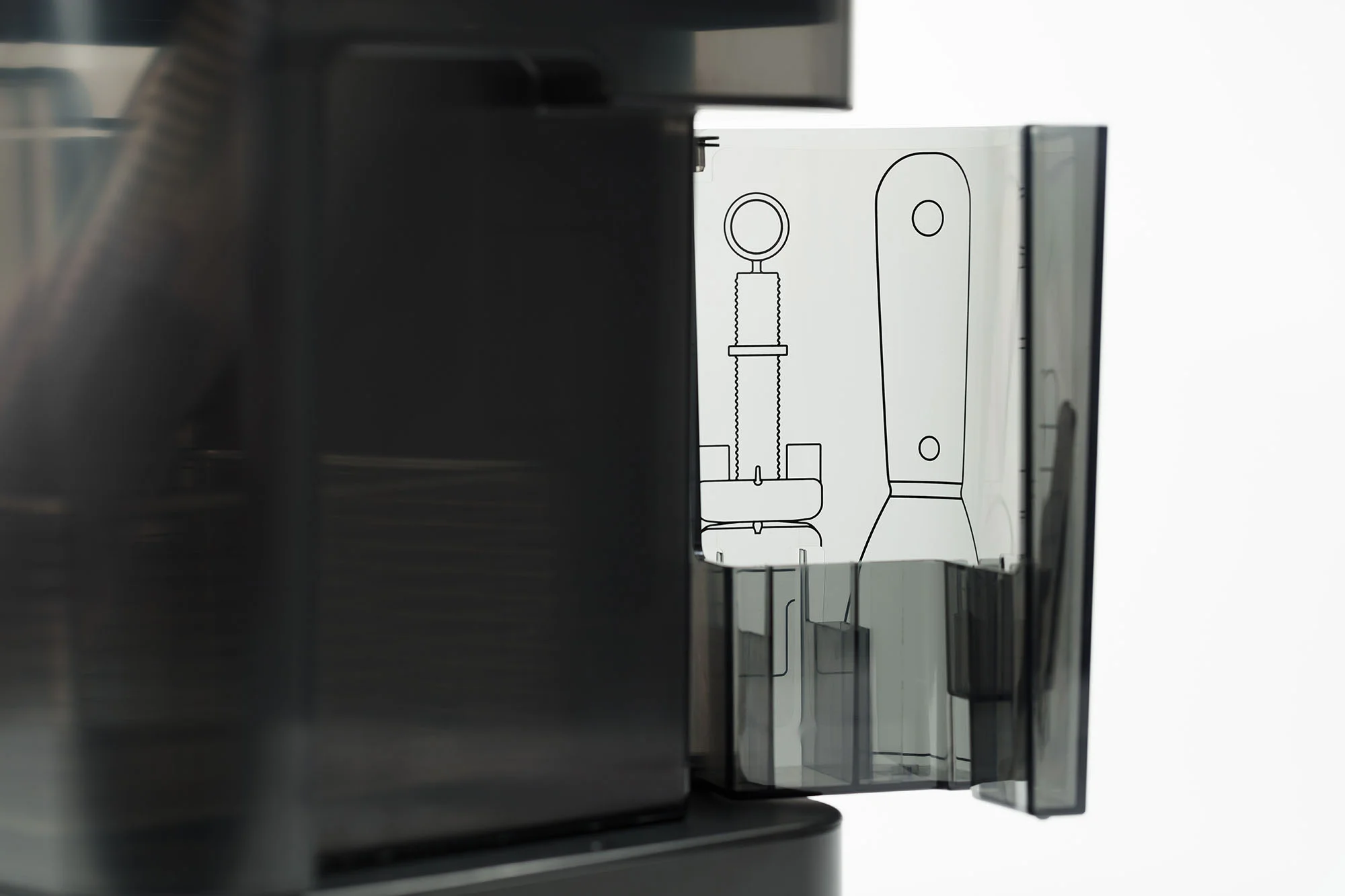
Form Wash has integrated flip out tool holders to store the hydrometer and tools used to remove parts and support structures.
Form Wash System Overview showing the tool holders in use